调节阀的故障分析及处理措施更新日期:2021-03-22
气动调节阀不动作
原因1:
无气源或气源压力过小
措施:
应首先检查气源(仪表空气)是否通畅,气源压力是否达到该阀使用要求。
原因2:
有气源,无输出信号气压力
措施:
1. 对机械控制器或定位器,应更机械压力控制器或定位器。
2.对机械控制器的气动调节阀,检查调节阀安装管路上介质的信号采集管路阀门是否全开或泄漏严重,如果有异常应及时处理。
原因3:
输出信号气压力正常,仍不动作。
措施:
1. 检查气动隔膜执行机构的隔膜是否有严重漏气现象,如果漏气,应及时更换隔膜及相关密封件。
2.如果检查隔膜完好没有漏气,则应是主阀阀芯与衬套、阀座卡死,应解体检查主阀,清理杂物。
3.阀杆弯曲变形严重,应解体检查主阀,根据检查情况更换处理。
4.信号气源管路有泄漏,检查处理漏点。
5.信号放大器故障或调整不当,主气源未通过放大器进入隔膜腔,应及时调整或更换放大器。
调节阀工作时产生调节震荡、控制不稳定
原因1:
气源压力变化较大或过滤器、减压阀工作不正常。
措施:
1.检查压缩空气系统运行状态。
2.检查更换过滤器或减压阀。
原因2:
气源压力稳定,信号压力不稳。
措施:
1.更换智能定位器后如果还不稳定,应对PID参数整进行整定。
2.对机械控制器或定位器,应更换机械控制器或定位器,并对控制器进行调定。
3.更换机械控制器或定位器后仍不稳定,应检查更换信号气源放大器,并进行调定。
原因3:
气源、信号压力均稳定,但调节阀工作仍不稳定。
措施:
1. 检查气动隔膜执行器的气密性。仔细检查驱动推杆密封是否有轻微漏气现象,如果存在漏气应解体更换密封;解体检查隔膜是否有划伤、刺伤而造成的轻微漏气现象,如有漏气应更换隔膜。
2.仔细检查定位器与主阀连接部位是否有间隙,应重新更换或紧固定位器与主阀的相关连接件。
3.用肥皂水仔细检查信号气管路是否有轻微漏气现象,一旦发现应及时处理。
4.信号气源放大器调定不合理,调整信号气源放大器平衡螺钉。
5.调节阀运动机构(包括主阀和气动隔膜执行器)阻力过大,应解体主阀,检查更换异常元件,包括阀芯、阀座、阀杆、阀杆密封及驱动推杆。
6.检查气动隔膜执行机构内压力平衡弹簧是否损坏,弹簧是否已疲劳变形,如果存在异常应更换压力平衡弹簧。
调节阀动作迟缓
原因1:
阀体内有黏物堵塞。
措施:
解体主阀体,清理阀体内黏物。
原因2:
阀杆填料变质硬化或石墨、石棉填料润滑油干燥。
措施:
解体主阀体,更换阀杆填料。
原因3:
填料加得太紧,摩擦阻力增大。
措施:
1. 将阀杆填料压紧螺母调松后,往复动作主阀多次,在将阀杆填料压紧螺母调整合适力矩。
2.如果措施1没有,更换阀杆填料,将阀杆填料压紧螺母调整合适力矩。
原因4:
阀杆不直导致摩擦阻力大。
措施:
主阀解体,更换阀杆。
原因5:
气动隔膜执行器隔膜或信号气管路有轻微漏气。
措施:
更换气动隔膜执行器隔膜,处理信号气管路漏气。
调节阀动作正常,工艺控制参数异常
原因1:
调节阀阀芯脱落。
措施:
解体检查调节阀主阀体,根据检查情况恢复阀芯脱落。
原因2:
调节阀阀芯与阀杆连接部位发生相对移位,但未脱开。
措施:
解体检查调节阀主阀体,根据检查情况恢复阀芯位置。
原因3:
调节阀阀杆断裂。
措施:
解体检查调节阀主阀体,更换阀杆。
原因4:
调节阀阀芯内有污物堵塞。
措施:
解体检查调节阀主阀体,清理阀芯内污物。
原因5:
被控制介质系统其他控制参数不合适,如介质流量、压力不在设计要求范围内。
措施:
调整系统控制参数在设计要求范围内。
阀友
检修时,该检查哪些部位呢?
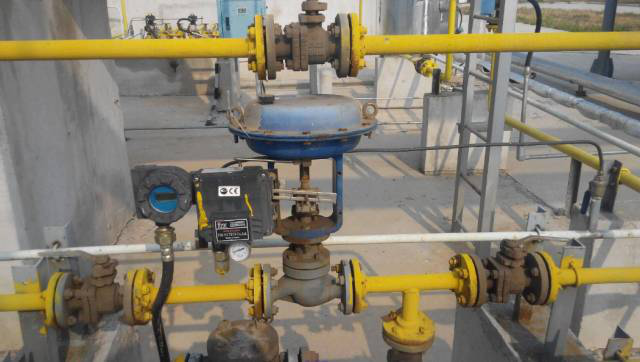
阀体内壁
在高压差和有腐蚀性介质的场合,阀体内壁、隔膜阀的隔膜经常受到介质的冲击和腐蚀,必须检查耐压耐腐情况。
阀芯
阀芯是调节阀的可动部件之一,受介质的冲蚀较为严重,检修时要认真检查阀芯各部是否被腐蚀、磨损。
特别是在高压差的情况下,阀芯的磨损因空化引起的汽蚀现象更为严重损坏严重的阀芯应予更换检查密封填料:检查盘根石棉绳是否干燥,如采用聚四氟乙烯填料,应注意检查是否老化和其配合面是否损坏。
阀座
因工作时介质渗入,固定阀座用的螺纹内表面易受腐蚀而使阀座松弛。
膜片及O型圈
易损件,检查是否老化。
填料
当调阀采用石墨或石棉为填料时,大约三个月应在填料上添加一次润滑油,以保证调阀动作灵活。
如发现填料压帽压得很低,则应补充填料;如发现聚四氟乙燥填料硬化,则应及时更换。
气源
对配有定位器的调阀要经常检查气源,保证气源品质,不含水及其它杂物。
原因1:
无气源或气源压力过小
措施:
应首先检查气源(仪表空气)是否通畅,气源压力是否达到该阀使用要求。
原因2:
有气源,无输出信号气压力
措施:
1. 对机械控制器或定位器,应更机械压力控制器或定位器。
2.对机械控制器的气动调节阀,检查调节阀安装管路上介质的信号采集管路阀门是否全开或泄漏严重,如果有异常应及时处理。
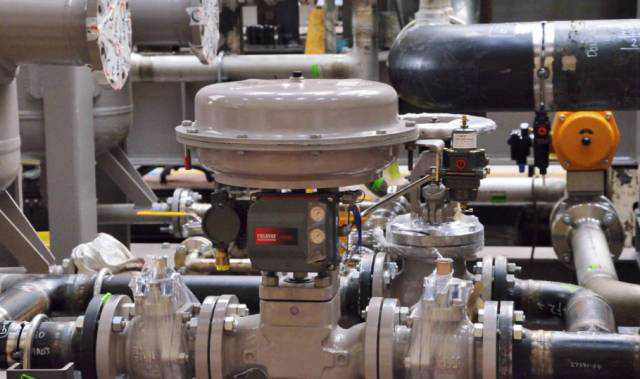
原因3:
输出信号气压力正常,仍不动作。
措施:
1. 检查气动隔膜执行机构的隔膜是否有严重漏气现象,如果漏气,应及时更换隔膜及相关密封件。
2.如果检查隔膜完好没有漏气,则应是主阀阀芯与衬套、阀座卡死,应解体检查主阀,清理杂物。
3.阀杆弯曲变形严重,应解体检查主阀,根据检查情况更换处理。
4.信号气源管路有泄漏,检查处理漏点。
5.信号放大器故障或调整不当,主气源未通过放大器进入隔膜腔,应及时调整或更换放大器。
调节阀工作时产生调节震荡、控制不稳定
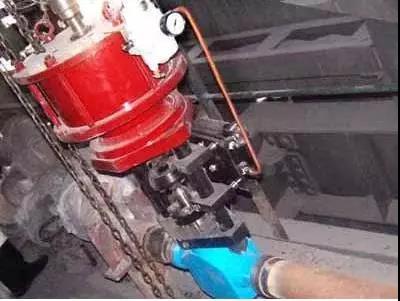
原因1:
气源压力变化较大或过滤器、减压阀工作不正常。
措施:
1.检查压缩空气系统运行状态。
2.检查更换过滤器或减压阀。
原因2:
气源压力稳定,信号压力不稳。
措施:
1.更换智能定位器后如果还不稳定,应对PID参数整进行整定。
2.对机械控制器或定位器,应更换机械控制器或定位器,并对控制器进行调定。
3.更换机械控制器或定位器后仍不稳定,应检查更换信号气源放大器,并进行调定。
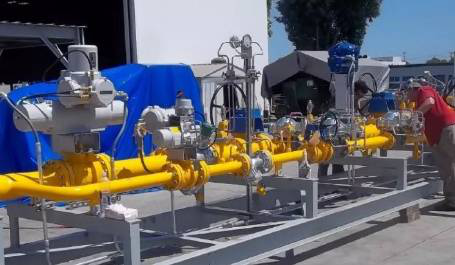
原因3:
气源、信号压力均稳定,但调节阀工作仍不稳定。
措施:
1. 检查气动隔膜执行器的气密性。仔细检查驱动推杆密封是否有轻微漏气现象,如果存在漏气应解体更换密封;解体检查隔膜是否有划伤、刺伤而造成的轻微漏气现象,如有漏气应更换隔膜。
2.仔细检查定位器与主阀连接部位是否有间隙,应重新更换或紧固定位器与主阀的相关连接件。
3.用肥皂水仔细检查信号气管路是否有轻微漏气现象,一旦发现应及时处理。
4.信号气源放大器调定不合理,调整信号气源放大器平衡螺钉。
5.调节阀运动机构(包括主阀和气动隔膜执行器)阻力过大,应解体主阀,检查更换异常元件,包括阀芯、阀座、阀杆、阀杆密封及驱动推杆。
6.检查气动隔膜执行机构内压力平衡弹簧是否损坏,弹簧是否已疲劳变形,如果存在异常应更换压力平衡弹簧。
调节阀动作迟缓
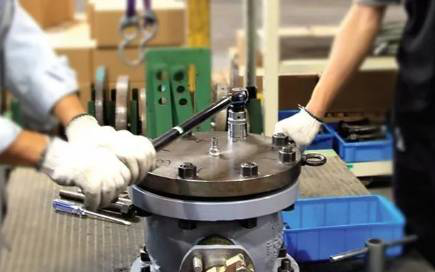
原因1:
阀体内有黏物堵塞。
措施:
解体主阀体,清理阀体内黏物。
原因2:
阀杆填料变质硬化或石墨、石棉填料润滑油干燥。
措施:
解体主阀体,更换阀杆填料。
原因3:
填料加得太紧,摩擦阻力增大。
措施:
1. 将阀杆填料压紧螺母调松后,往复动作主阀多次,在将阀杆填料压紧螺母调整合适力矩。
2.如果措施1没有,更换阀杆填料,将阀杆填料压紧螺母调整合适力矩。
原因4:
阀杆不直导致摩擦阻力大。
措施:
主阀解体,更换阀杆。
原因5:
气动隔膜执行器隔膜或信号气管路有轻微漏气。
措施:
更换气动隔膜执行器隔膜,处理信号气管路漏气。
调节阀动作正常,工艺控制参数异常
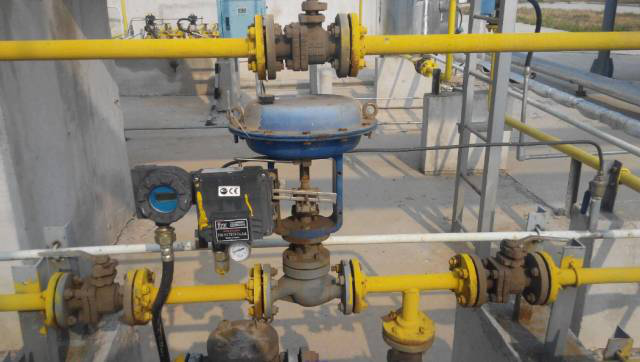
原因1:
调节阀阀芯脱落。
措施:
解体检查调节阀主阀体,根据检查情况恢复阀芯脱落。
原因2:
调节阀阀芯与阀杆连接部位发生相对移位,但未脱开。
措施:
解体检查调节阀主阀体,根据检查情况恢复阀芯位置。
原因3:
调节阀阀杆断裂。
措施:
解体检查调节阀主阀体,更换阀杆。
原因4:
调节阀阀芯内有污物堵塞。
措施:
解体检查调节阀主阀体,清理阀芯内污物。
原因5:
被控制介质系统其他控制参数不合适,如介质流量、压力不在设计要求范围内。
措施:
调整系统控制参数在设计要求范围内。
阀友
检修时,该检查哪些部位呢?
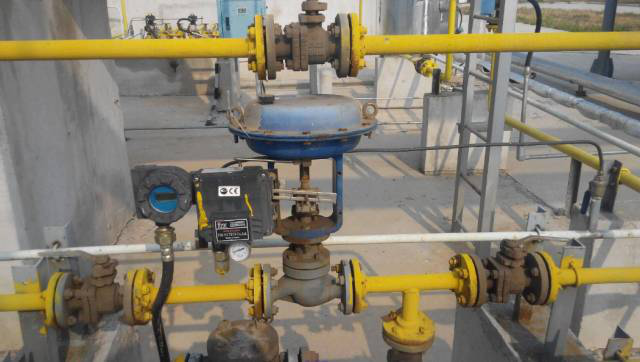
阀体内壁
在高压差和有腐蚀性介质的场合,阀体内壁、隔膜阀的隔膜经常受到介质的冲击和腐蚀,必须检查耐压耐腐情况。
阀芯
阀芯是调节阀的可动部件之一,受介质的冲蚀较为严重,检修时要认真检查阀芯各部是否被腐蚀、磨损。
特别是在高压差的情况下,阀芯的磨损因空化引起的汽蚀现象更为严重损坏严重的阀芯应予更换检查密封填料:检查盘根石棉绳是否干燥,如采用聚四氟乙烯填料,应注意检查是否老化和其配合面是否损坏。
阀座
因工作时介质渗入,固定阀座用的螺纹内表面易受腐蚀而使阀座松弛。
膜片及O型圈
易损件,检查是否老化。
填料
当调阀采用石墨或石棉为填料时,大约三个月应在填料上添加一次润滑油,以保证调阀动作灵活。
如发现填料压帽压得很低,则应补充填料;如发现聚四氟乙燥填料硬化,则应及时更换。
气源
对配有定位器的调阀要经常检查气源,保证气源品质,不含水及其它杂物。
上一篇:如何正确选用蒸汽电磁阀? 下一篇:气动执行器原理、分类、选型